Дипломная работа
«Технологический процесс ремонта тележки грузового вагона»
- 100 страниц
Введение ….… 6
1. Анализ базового технологического процесса ремонта тележки грузового
вагона ….….…. 9
1.1 Анализ конструкции тележки грузового вагона ….…. 9
1.2 Анализ существующих способов ремонта и выбор способа
восстановления подпятника ….….… 15
1.3 Анализ базового технологического процесса ремонта тележки грузового
вагона ….….…. 18
2 Разработка технологического процесса ремонта надрессорной балки ….… 29
2.1 Анализ существующих способов ремонта и выбор способа восстановления
подпятника … 29
2.2 Сущность технологического процесса наплавки типовых деталей ….…. 40
2.3 Определение параметров технологического процесса восстановления
подпятника … 47
2.4 Выбор оборудования и проектирование технологической оснастки для
наплавки и механической обработки подпятника …. 59
3 Технико-экономические расчеты ….…. 65
3.1 Нормирование технологических операций для наплавки и механической
обработки подпятника ….…. 65
3.2 Оценка технико-экономической эффективности ремонта надрессорной
балки наплавкой с последующей механической обработкой подпятника .… 67
4. Обеспечение требований безопасности труда в конструкции оборудования . 80
4.1 Характеристика опасных зон на оборудовании ….…. 80
4.2 Определение наличия и эффективности действия технических средств,
обеспечение безопасности обслуживания оборудования ….… 84
4.3 Эргономический анализ организации рабочего места на оборудовании .… 88
4.4 Выводы и предложения с разработкой конструкции технического средства
(устройства безопасности) ….…. 91
Заключение ….… 95
Список использованной литературы ….….…. 97
Спецификации ….… 101
Железнодорожный транспорт составляет основу транспортного комплекса Российской Федерации. Перед ним в период реформирования поставлены две кардинальные задачи: первое – снижение эксплуатационных расходов на осно-ве дальнейшего совершенствования структуры управления и научно-технического прогресса, вторая – создание и оснащение железных дорог техническими средствами нового поколения, не уступающими по своим параметрам лучшим современным образцам. Задача обеспечения снижения эксплуатационных ресурсов на железнодорожном транспорте требует перевода вагонных депо на новые ресурсы и энергосберегающие технологии [1].
Западно-Сибирская железная дорога является сегодня лидером по внедрению прогрессивных технологий при деповском ремонте грузовых вагонов. Характерной ее особенностью является то, что она объединяет протяженный участок Транссибирской магистрали с мощными сортировочными и участковыми станциями Входная, Московка, Инская и развитой погрузочный участок Кузбасса с разветвленной сетью погрузочных станций.
В настоящее время перед железнодорожным транспортом стоят такие задачи, как повышение надежности уже существующего устаревшего вагонного парка; увеличение гарантийных участков; повышение безопасности движения поездов. При всё возрастающих скоростях движения, увеличении массы грузовых поездов вопросы надежности буксы встают наиболее остро [10].
Одной из задач, вставшей перед железнодорожными хозяйствами, стано-вится поддержание подвижного состава в рабочем состоянии при ограниченных финансовых ресурсах [17]. Поэтому процесс восстановления изношенных деталей является на сегодняшний день актуальной задачей.
Восстановление изношенных деталей подвижного состава обеспечивает экономию высококачественного материала, топлива, энергетических и трудовых ресурсов. Для восстановления трудоспособности изношенных деталей требуется в 5-8 раз меньше технологических операций по сравнению с изготовлением новых деталей [20].
Однако ресурс восстановленных деталей по сравнению с новыми, во мно-гих случаях, остается низким. В то же время имеются такие примеры, когда ресурс восстановленных прогрессивными способами, в несколько раз выше ресурса новых деталей [25].
Основа повышения качества – применение передовых технологий восстановления деталей.
Тележка грузового вагона работает в очень сложных и тяжелых условиях. Процесс изнашивания её основных частей является нежелательным, но неизбежным. К числу основных недостатков тележки модели 18-100 является недостаточная износостойкость подпятникового узла надрессорной балки, что вызывает необходимость частых ремонтов узла сваркой и уменьшает безотказ-ность тележки. Кроме того, повышенные износы в данном узле ухудшают ди-намико-прочностные характеристики вагонов, что отрицательно сказывается не только на состоянии самих вагонов, но и увеличивает износ колес и рельсов.
При восстановлении надрессорной балки возникает необходимость изыскания новых, более прогрессивных способов восстановления, которые смогли бы повысить её ресурс при сравнительно низких затратах.
Целью дипломного проекта является комплексное исследование передовых технологий восстановления деталей тележки грузового вагона; выбор наи-лучшего способа восстановления одной из ответственных деталей – надрессор-ной балки; определение путей улучшения применяемого на предприятии технологии ремонта и оценка эффективности проводимых восстановительных работ.
Для решения этой цели в работе поставлены и решены следующие задачи:
– проанализировать технологический процесс ремонта тележки грузового вагона и различные способы восстановления её работоспособности;
– разработать технологический процесс ремонта надрессорных балок;
– модернизировать оборудование для восстановления подпятникового узла надрессорных балок;
– дать технико-экономическаю оценку эффективности ремонта надрессорной балки.
Для выполнения указанных задач использованы исходные данные о подвиж-ном составе железных дорог действующего эксплуатационного предприятия.
Объектом исследования работы является Вагонное депо Омск – Сортировоч-ный – структурной единицы Новосибирского отделения железной дороги – фи-лиала ОАО «РЖД».
Предметом исследования стал процесс ремонта надрессорной балки тележки грузового вагона модели 18-100.
Методологической основой исследования являются законодательные акты, инструктивные материалы, монографии, статьи отечественных и зарубежных авторов, учебники и учебные пособия.
При написании работы использовались следующие методы: монографическое исследование, наблюдение, детализация, сравнительный анализ, табличный и графический методы.
Работа выполнена с помощью программных продуктов WORD и EXCEL и KOMPAS – 3D V8.
При разработке технологического процесса сначала определяют износ и по-вреждения, пользуясь рабочими чертежами и техническими условиями на восстанавливаемую деталь. Затем выбирают наиболее рациональный способ устранения неисправностей с учетом вида материала, термической обработки и конструктивных особенностей детали, а также условий ее работы в сопряжении с другой деталью. Учитывают технические возможности предприятия.
Ремонт надрессорной балки
Надрессорные балки перед ремонтом и дефектацией очищают от грязи, от-слоившейся ржавчины и разрушившегося лакокрасочного покрытия, обмыва-ют в моечной машине, осматривают на возможность обнаружения трещин, отколов и износов. Опорную поверхность подпятника балки очищают до металлического блеска [21].
При осмотре и дефектации надрессорной балки определяют целостность верхних, нижних поясов, вертикальных стенок и колонки при её наличии, опорной части подпятника, исправность приливов для колпаков скользунов и износы трущихся поверхностей.
Поперечные трещины во внутренней колонке, расположенные не ниже 250 мм от зоны внутренней поверхности нижнего пояса надрессорной балки, не-зависимо от их длины ремонту не подлежат. Внутреннюю поверхность балки осматривают с подсветкой через технологические окна верхнего и нижнего поя-сов.
При капитальном или деповском ремонте под вагон подкатывают тележки с надрессорными балками, с установленными износостойкими элементами по проекту М
1698 ПКБ ЦВ. Оставшийся срок службы надрессорных балок должен быть не менее чем до следующего капитального или деповского ремонта вагона соответственно или до окончания оставшегося срока службы вагона.
После определения объема ремонта все дефекты подпятника надрессорной балки должны быть отремонтированы.
При плановых видах ремонта разрешается заваривать трещины в подпятнике надрессорной балки. Суммарная длина трещин в подпятнике допускается не более 250 мм, если трещины кольцевые прерывистые, расположенные в разных секторах, на расстоянии от центра не ближе 80 мм.
Ранее установленные в подпятник износостойкие кольца (полукольца) уда-лить станочной обработкой.
Диаметр подпятника определяют от верхней горизонтальной поверхности наружного бурта на глубине 10 мм с учетом конусности 1:12,5 (4 градуса 36 минут).
У надрессорной балки выпуска до 1986 года и с 1986 года диаметр подпятника - 302,5 +1,5 мм.
Контроль диаметра подпятника надрессорной балки производить штанген-циркулем ШЦ-III-400-0,1 ГОСТ 166-89.
Контроль глубины подпятника надрессорной балки производить штанге-ном подпятника проект Т914.06 ПКБ ЦВ или штангенциркулем ШЦ-I-125-0.1 ГОСТ 166-89.
У надрессорной балки, изготовленной до 1986 г. с глубиной подпятника 25 мм изношенные опорная поверхность, наружный и внутренний бурты подпятника восстанавливают согласно Инструкций ЦВ 201-98, ТИ-05-01-03/НБ и ТИ-05-01/2003НБ износостойкой наплавкой с обеспечением твёрдости 240 – 300 НВ, с последующей станочной обработкой подпятника до чертёжных размеров с обеспечением конусности внутренней поверхности наружного бурта 1:12,5 и диаметром 302,5+1,5 мм на глубине 10 мм.
У надрессорной балки, изготовленной с 1986 г., с глубиной подпятника 30 мм с изношенными опорной поверхностью, наружным и внутренним буртами подпятника, наружный и внутренний бурты наплавляют из-носостойкой наплавкой согласно Инструкций ЦВ 201-98, ТИ-05-01-03/НБ и ТИ-05-01/2003НБ с обеспечением твердости 240 – 300 НВ.
Подпятник растачивается на глубину 36±1 мм с обеспечением конусности внутренней поверхности наружного бурта 1:12,5 и диаметром 302,5+1,5 мм на глубине 10 мм.
На обработанную плоскую опорную поверхность подпятника устанавлива-ется прокладка по чертежу М 1698.01.005 диаметром 298-1,3 мм фаской вниз.
При поступлении надрессорной балки с установленной ранее прокладкой, подпятник с глубиной 36±1 мм, имеющий износы на наружном и внутреннем буртах, выработки наружного бурта от прокладки, наплавляются согласно Инструкций ЦВ 201-98, ТИ-05-01-03/НБ и ТИ-05-01/2003НБ износостойкой наплавкой с обеспечением твердости 240 – 300 НВ с последующей станочной обработкой согласно чертежу М 1698.01.000 СБ и обеспечением конусности внутренней поверхности наружного бурта 1:12,5 с последующей постановкой прокладки по чертежу М 1698.01.005.
Оставшаяся толщина опорной поверхности подпятника не менее 18 мм оп-ределяется ультразвуковыми толщиномерами типа УТ-93П, А 1207, А 1208, ТУЗ-1, ТУЗ-2.
Основной проблемой, стоящей перед железнодорожными компаниями, является сокращение эксплуатационных расходов. Одна из наиболее значимых статей этих расходов - затраты на техническое обслуживание и ремонт подвижного состава, которые включают много трудоемких операций, зачастую выполняемых в неблагоприятных условиях. Поэтому механизации и автоматизации технологического процесса обслуживания и ремонта подвижного состава уделяется особое внимание.
Эти операции имеют свою специфику и практически не встречаются в современном машиностроительном производстве [6].
В результате дипломного проектирования была разработан технологиче-ский процесс восстановления подпятника надрессорной балки тележки грузового вагона с применением специального оборудования как для сварочных (наплавочных) операций, так и для операций механической обработки подпятника после наплавки.
При дипломном проектировании были рассмотрены передовые технологии восстановления деталей тележки грузового вагона произведён выбор наилучшего способа восстановления одной из ответственных деталей – надрессорной балки
Было обосновано и доказано, что применение наплавки под слоем флюса выгодно отличается по качеству наплавляемого слоя металла от таких видов наплавки, как ручная дуговая и автоматическая в среде защитных газов.
В результате применения автоматической наплавки под слоем флюса снижается процент потерь от брака, влияние вредных факторов на работников, трудоёмкость ремонтных работ.
Несмотря на то, что проектируемый технологический процесс требует приобретения нового оборудования, из расчёта годового экономического эффекта видно, что дешевле балку ремонтировать, чем покупать новую. Также видно, что предлагаемый технологический процесс намного эффективней базового. Это объясняется тем, что в предлагаемом технологическом процессе надрессорную балку обрабатывают на специальном станке, с использованием специального инструмента, что снижает трудоёмкость механической обработки надрессорной балки после наплавки. В базовом технологическом процессе применяют универсальное оборудование и инструмент. Коэффициент загрузки станка в предлагаемом технологическом процессе намного больше, чем в базовом (в предлагаемом технологическом процессе выбран станок, резервы которого полностью используются).
Экономический эффект также достигается за счёт наплавочных работ. На-плавка подпятника ручной дуговой сваркой, либо в среде защитных газов - дело очень длительное и трудоёмкое. Часто работа бракуется после дефектации, так как в наплавленном слое встречаются разные включения и пустоты. Наплавка на специальной установке позволяет не только экономить время, но ещё и получить готовую поверхность подпятника, которую можно получить любой (нужной) твёрдости, шероховатости, что сказывается на качестве отремонтированного подпятника.
Рассчитанный годовой экономический эффект от внедрения нового техно-логического процесса составляет Эг = 9537260,00 руб.
Таким образом, применение специального оборудования для наплавки и механической обработки подпятников надрессорных балок тележек подвижного состава железных дорог целесообразно.
1. Авраменко В. И., Шейко О. И. Вопросы организации и экономики сва-рочного производства. – Киев.: Наукова думка, 1983. – 72 с.: ил.
2. Автоматизация сварочных процессов /Под ред. В.К. Лебедева, В.П. Чер-ныша. – К.: Вища школа, 1986. – 296 с.
3. Акулов А.И. и др. Технология и оборудование сварки плавлением. – М.: Машиностроение, 1977. – 432 с.
4. Алешин Н.П. Контроль качества сварочных работ. – М.: Высш. шк., 1986. – 324 с.
5. Анисимов П. С. Испытания вагонов: монография / П. С. Анисимов. - М. Маршрут, 2004. - 197 с.
6. Арферов А.К., Петров И. В. Обеспечение работоспособности строи-тельных машин. – М.: Стройиздат, 1980, – 136 с.
7. Болотин М. М. Системы автоматизации производства и ремонта вагонов: учебник для ж.-д. вузов / М. М. Болотин, В. Е. Новиков ; утв. Департаментом кадров и учеб. завед. МПС России. - М. : Маршрут, 2004. - 310 с
8. Бондин И. Н. Справочник сварщика. – М. – Л.: Машиностроение, 1965. – 400 с.: ил.
9. Браткова О.Н. Источники питания сварочной дуги. – М.: Высшая школа, 1982. – 181 с.
10. Вагонное хозяйство : учеб. для студ. вузов ж.-д. трансп. / утв. Деп. кадров и учеб. завед. МПС России ; под ред. : П. А. Устича. - М. : Маршрут, 2003. - 560 с.
11. Волченко В.Н. Контроль качества сварных конструкций. – М.: Машино-строение, 1986. – 264 с.
12. Вредные вещества в промышленности. Справочник / Под ред. Н.В. Лаза-рева. – М.: Химия, 1971. – 654 с.
13. Геворкян В. Г. Основы сварочного дела. – М.: Высшая школа, 1979. – 207 с.; ил.
14. ГОСТ 12.0.003-74. Опасные и вредные производственные факторы. Классификация. – М.: Изд-во стандартов, 1974.
15. ГОСТ 12.1.005-88 ССБТ. Общие санитарно-гигиеничесские требования к воздуху рабочей зоны. – М.: Изд-во стандартов, 1988.
16. ГОСТ 12.4.021-75 ССБТ. Системы вентиляционные. Общие требования безопасности. – М.: Изд-во стандартов, 1976.
17. Гридюшко В. И., Бугаев В. П., Криворученко И. З. Вагонное хозяйство: Учебное издание для вузов. М.: Транспорт, 1988. – 295 с.
18. Инструкция по технике безопасности при производстве газосварочных работ / Всерос. об-ние межколхоз. строит. орг.; Республ. проектно-технол. произв. об-ние «Росоргтехстрой». – Омск: Обл. тип., 1980. – 14 с.; 20см.
19. Комплект документов на типовой технологический процесс ремонта те-лежки модели 18-100. ТК-287-2007.21. Короткова Г.М. Источники питания технологических установок. Уч. пособие. – Тольятти: АНО ГАЦ СВР, 2001. – 58 с.
20. Либман А.З., Демченков Г.И. Вагонное хозяйство. Пособие по дипломному проектированию. М.: Транспорт, 1983. – 103 с.
21. Лисевич Т. В.Машины вагоноремонтного производства : учеб. пособие / Т. В. Лисевич, Е. В. Александров. Ч. 2. - Самара : СамГАПС, 2003. - 43 с
22. Лукашук В. С. Нестандартное оборудование вагоносборочного производства. Конструкция, проектирование, расчет : учеб. пособие для вузов ж.-д. трансп. / В. С. Лукашук ; рек. Управ. кадров, учеб. завед. и правов. обеспечения Федер. агентства ж.-д. трансп. - М. : Маршрут, 2006. - 208 с.
23. Малышев Б. Д., Гетия И. Г. Безопасность труда при выполнении сва-рочных работ в строительстве. – М.: Стройиздат, 1988. – 88 с.: ил.
24. Методика выполнения измерений надрессорной балки, боковых рам, пружин и рессорного комплекта при проведении плановых видов ремонта тележек 18 – 100. РД 32 ЦВ 050-2005.
25. Мотовилов К.В. Технология производства и ремонта вагонов. Учебник. – М.: маршрут, 2003. – 382 с.
26. Нефедов Н.А., Осипов К.А. Сборник задач и примеров расчёта по ре-занию металлов и режущему инструменту. – М.: Машиностроение, 1984. – 156 с.
27. Общемашиностроительные нормативы режимов резания для техниче-ского нормирования работ на металлорежущих станках ЦБПНТ. – М.: Машиностроение, 1974.
28. Охрана труда в машиностроении / Под ред. Е.Я. Юдина. – М.: Машино-строение, 1983. – 431 с.
29. Охрана труда в электроустановках: Учебник для вузов / Под ред. Б.А. Князевского. – М.: Энергия, 1977. – 319 с.
30. Пастухов И. Ф. Конструкция вагонов : учеб. для техн. ж.-д. трансп. / И. Ф. Пастухов, В. В. Пигунов, Р. О. Кошкалда ; утв. Деп. кадров и учеб. завед. МПС России. - 2-е изд. - М. : Маршрут, 2004. - 504 с
31 Правила технической эксплуатации железных дорог Российской Федера-ции. М.: Транспорт, 2000. – 96 с.
32. Режимы резания: Справочник: в 2 т./ под ред. Локтева. – М.: Машино-строение, 1988. – 274 с.
33. Руководящий документ. Деповской ремонт грузовых вагонов ЦВ-587
34. Руководящий документ. Ремонт тележек грузовых вагонов. РД 32 ЦВ 052-2005.
35. Руководящий документ. Ремонт тележек грузовых вагонов модели 18-100 с установкой износостойких элементов в узлах трения. РД 32 ЦВ 072-2005.
36. Руководящие документы по неразрушающему контролю РД 32.174-2001, РД 32.149-2000, РД 32.159-2000,
37. Сварка в машиностроении. Справочник в 4-х т. / Редкол.: Г. А. Николаев (пред.) и др. – М.: Машиностроение, 1978. – т. 1 / Под ред. Н. А. Ольшанского. 1978. – 504 с.: ил.
38. Сварка в машиностроении. Справочник в 4-х т. / Редкол.: Г. А. Николаев (пред.) и др. – М.: Машиностроение, 1978. – т. 2 / Под ред. А. И. Акулова. 1978. – 462 с.: ил.
39. Сварка и свариваемые материалы. В 3-х томах. Т-1. Свариваемость материалов. Спр. изд. / Под ред. Э.Л. Макарова. – М.: Металлургия, 1991. – 528 с.
40. Смольянинов В. С. Технология производства запасных частей и ремонта машин в 2 ч. / Под ред. Е.М. Стружестраха. – Омск: Типография ОмГУПСа, 1999. – Ч. 1. – 54 с.
41. Смольянинов В. С. Технология производства запасных частей и ремонта машин в 2 ч. / Под ред. Е.М. Стружестраха. – Омск: Типография ОмГУПСа, 1999. – Ч. 2. – 36 с.
42. Справочник нормировщика-машиностроителя: в 2 т. / Под ред. Е.М. Стружестраха. – М.: ГОСИздат, 1961. – Т,2. – 892 с.
43. Справочник по обработке металлов резанием. Абрамов Ф.Н. и др. – К.: Техника, 1983. – 346 с.
44. Справочник технолога-машиностроителя / Под ред. Касиловой А.Г., Мещерякова В.К. – М.: Машиностроение, 1985. – 362 с.
45. Средства защиты в машиностроении. Расчет и проектирование. Спра-вочник / Под ред. С.В. Белова – М: Машгиз, 1989. – 359 с.
46. Технология производства и ремонта вагонов : учеб. для вузов ж.-д. трансп. / утв. Деп. кадров и учеб. завед. МПС России; под ред. : К. В. Мотовилова. - М. : Маршрут, 2003. - 382 с.
47. Цепенев Р.А. Автоматизация сварочных процессов: Учебное пособие. – Тольятти: ТолПИ, УКЦ «Конкурс», 1990. – 107 с.
48. Электросварочное оборудование. Автоматы, головки, установки для дуговой сварки. Системы и аппаратура управления установками дуговой свар-ки. – М.: АО Стандартэлектро, 1993. – 91 с.
49. Электросварочное оборудование. Комплектующие изделия оборудования для дуговой сварки. – М.: АО Стандартэлектро, 1993. – 43 с.
чертежи в программе Компас:
1. Тележка грузового вагона
2. Балка надрессорная
3. Планировка наплавочного участка
4. Установка для наплавки подпятника надрессорной балки
5. Операционная карта
6. Схема наплавки
Тема: | «Технологический процесс ремонта тележки грузового вагона» | |
Раздел: | Транспорт | |
Тип: | Дипломная работа | |
Страниц: | 100 | |
Цена: | 13000 руб. |
Закажите авторскую работу по вашему заданию.
- Цены ниже рыночных
- Удобный личный кабинет
- Необходимый уровень антиплагиата
- Прямое общение с исполнителем вашей работы
- Бесплатные доработки и консультации
- Минимальные сроки выполнения
Мы уже помогли 24535 студентам
Средний балл наших работ
- 4.89 из 5
написания вашей работы
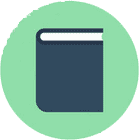
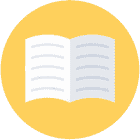
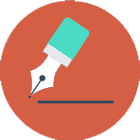
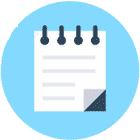
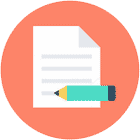
682 автора
помогают студентам
23 задания
за последние сутки
10 минут
среднее время отклика
Курсовая работа
«Буксовый узел грузового вагона. Деталь корпус буксы.»Курсовая работа
«Разработка технологического процесса отделки корпусной мебели методом имитационной отделки и лаком МЛ-2111»Курсовая работа
«Организация торгово-технологического процесса в магазине»Курсовая работа
«Технология машиностроения. Технологический процесс механической обработки детали»Дипломная работа
«Совершенствование технологического процесса механической обработки детали "Корпус подшипника"»